
HIGH END PARTS: HOW WE MAKE THE BEST
HIGH END PARTS: HOW WE MAKE THE BEST
WHO • WHY • WHEN:
THE GOAL FOR PERFECTION
My name is Joe Lala. I am the founder/president of Dewla Dezign LLC.
​
I founded Dewla Dezign when I was just 19 years old, but in all reality my path to making high end performance parts started much earlier in my life.
​
THE LATE 90's:
Like many kids my age who had a passion for sports cars of the time, I found myself devouring as much information as I could. My face constantly planted in magazines such as Sport Compact Car, and all the other variants of the time. Getting yelled at by my teachers for lusting over these machines in class- only a 6th grader and white collar upper management of a contemporary U.S could imagine them sitting in their garage when they got home. I would salivate over the FD RX7, MKIV SUPRA and 300zx. These were the dream cars for the kids of my generation
​
THE SPARK:
​
The truth is, I don't really know what the initial spark was for me with high performance cars. I loved the way they looked, the way they sounded and what they could do. There's something about so many functional parts working in harmony to complete one task that I was drawn to. There's a true art about a performance vehicle, and that art can be tailored to become a reflection of oneself. One fine way to experience the world, as it experiences you.
​
​


THE SHOP:
​
Growing up in a creative environment probably didn't hurt either. Most males on my fathers side of the family were engineers or machinist and typically could be found in the machine shop at the family business. It was quite the variety there. My father ran a diesel/gasoline repair shop on one side of the large facility. He also built drag and offset chassis race cars. On the other side of the shop was an automated silk screen business and a full blown machine shop.
​
I never came to fully understand any of these trades, but I did get to learn most of the fundamentals about all of them while I was there. I was fortunate to have access to this wide dynamic range of knowledge, and I still put the plethora of that knowledge to use until this day.
​
I BOUGHT A Z CAR:
​
Just before I turned 19, I finally bought one of my dream cars. A 1990 300zx Twin Turbo - that didn't run..
​
Shortly after, I decided to pull the engine and proceed with a full overhaul.
​
While I was slowly ordering parts for my car, I noticed that a lot of them were not the quality advertised, while paying top dollar for them to boot. I was a broke kid, so when I would finally get one part after partitioning several pay checks to afford it. I would be devastated when it was not up to par.
​
Then I had a thought.. I can make this.. I can make this and make it perfect.
​
​
​
​
​
​
​
​
​
​
​
​
​
​
​
​
​

QUALITY CONTROL & THE GOLDEN RULE:
​
Being very particular about the condition in which I wanted to receive parts when they arrived on my doorstep, I knew right off the start that one of the founding principles of my company would be that quality always comes first.. My customers would love opening up their packages and be proud to install my parts on their piece of collective art. This seems hard for many, but has always been easy for me. When you are passionate about what you do, It's easy to treat each piece as your own and do right. I still personally hand polish all of my parts and inspect them prior to them leaving my shop to this day. I have tried to outsource this many times over the last decade, but I always just end up refinishing them myself anyway- Perfection Does Exist
​
Just put it this way, I have NO problem scrapping parts.. Most of the time I cannot monetarily afford to do this, but I do it anyway because I know that it is the right thing to do. I will lose money before I send out products that are not perfect- PERIOD. Regroup, and figure out how to do it better the next time. I'm convinced that it is one of the few reasons to why my company is still in business today..
​
CUSTOMER SERVICE:
​
One of the biggest errors I see in most businesses is actually one of my easiest feats. As far as returns go, I can literally count on one hand to how many I have had in the span of 12 years. After thousands of parts have been delivered world wide. How many companies can say that? Probably almost zero.. Being that I put a great deal of effort into my quality control procedures, my life is a lot easier in this department.
​
My company is generally known for two things: High end quality American made parts and unmatched customer service.
​
If there is ever a quality issue with a part, I only ask questions to help me to do my job better.
​
You will get a new part if it is defective upon arrival in anyway.
​
I will always help my customers to the best of my knowledge, even if that means getting them in touch with the right person that may know more about that particular subject.
​
​
​
​
​
​
​
​
​
​
​
​
​
​
​
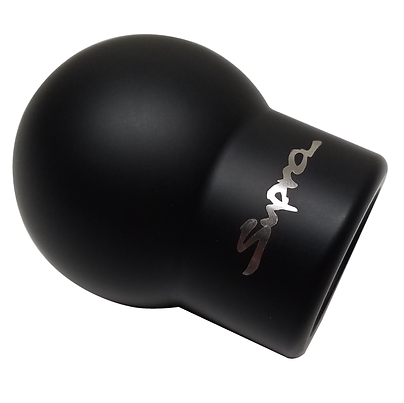
RESEARCH & DEVELOPMENT:
​
We spend a lot of time perfecting our parts. We ask more questions than most manufactures would ever consider, let alone perform in R&D.
​
We test every part extensively prior to hitting the market. Some products see as much as a two years of R&D prior to release.
​
SOURCES:
​
We always have and always will source all of our raw materials from American manufactures.
​
All of our parts are made on precision Okuma Crown CNC Lathes and Bridgeport mills.
​
UNIQUE METHODS THAT SET US APART:
​
For all of our tapping endeavors, we utilize thread forming press taps, opposed to standard cutting taps. These taps are VERY expensive and break often especially when being utilized in stainless steel.
​
Unlike cutting taps that require pre-drilled to full bore spec before initiation of the tap, thread forming taps displaces this excess material outward into the bore. Making much tighter tolerance threads, that have a very smooth threading action and clean burnished finish to them. The cold-worked threads generally last much longer to standard taps and perform flawlessly with repeat on and off threading, Not even our aluminum shift knobs have ever been returned for stripped threads. Which we honor for a lifetime even in they do..
​
FINISHES:
​
Our finishing process varies slightly from product to product. We have recently switched away from any anodize finishes to a more durable Cerakote™ finish. We find that this finish is superior in many ways to anodize, but like any coating, is still not impervious to being marred. We have tried nearly every coating under the sun that we know of and so far, this has been the best yet. It is also the most expensive, but we are willing to take the hit, in order to provide a better product.
​
​
​
​
For polishing, we use a 4 step process that generally takes around 30 minutes to 1 hour to complete one shift knob. Yes.. That is 30 minutes to 1 hour. In this process the part will see 3 different compounds working in a downward succession in grit. It's not polished until you can vividly see the pours of your skin in it's reflection.
​
We also have some proprietary finishing methods that we have figured out over the years that minimize light surface scratches. This is the final step prior to final inspection.
​
We choose classy over flashy. All of our designs are suited towards someone who wants a performance feel, with a contemporary / clean / professional look.
​
Unlike ANY OTHER shift knob manufacture that we know of, we are the only company that makes shift knobs specifically by vehicle. Not just a multitude of threaded inserts with different thread pitches and small dictation over height. This part is MADE FOR YOUR EXACT CAR. They will sit lower, cleaner and more comfortable than any other manufactures part on the market. Each shift knob is designed just for the perfect height of the vehicle it is designed for.
​
ATTENTION TO DETAIL:
​
Attention to detail is paramount for us here at Dewla Dezign. I cannot stress that enough. While developing the new Cold Air Guide for the 370z long tube intake systems, a year of R&D process took place. How do we make this part extremely effective, extremely affordable and extremely easy to install. How do we accommodate all aftermarket intakes,oil coolers, radiators and all the different trims of the 370z etc etc. The list was long, especially for a shot in the dark. We didn't know if it was going work.. How do we even really test it? We would need tools only the likes of F1 racing teams have access to.
We still don't understand it's full functionality and therefore it's full capabilities two years later. The results vary quite drastically every time we test it. We have seen anywhere for 0 gains all the way to 10whp gains depending on air speed, humidity, supporting mods etc. There's so many variables in a part that is so dependent on ambient everything. We know the 370z makes an average of 3 to 9whp less when tested with the front fascia on. That was proven long before this product was even brainstormed. So the hypothesis was already there for us when we started. How do we address this issue. 3rd party testing seemed to be the best way to go about it.
So we sent it out to several different Z specific shops to get tested and the results were different from every single one. Which left us with the conclusion that every atmospheric conditions were completely different in each testing facility. We know that it does not benefit well with high humid index, which makes sense. Testing is still being done to this day. We know it works, we just don't understand it to it's full degree :YET

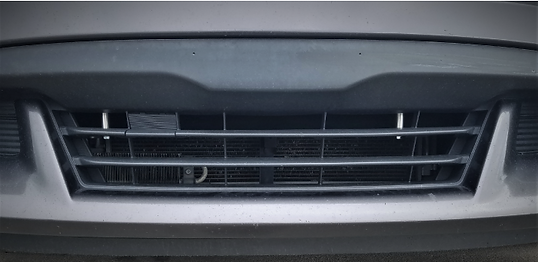
FOR THE FUTURE:
​
We are excited to break into new makes and models of vehicles. The Z car chassis has always been our staple, but there are many cars we would love to manufacture
pristine parts for. 2018 launched right with the latest product for the MKIV Supra. This is a big project taking underway. We found out very quickly why nobody; at least state side, had ventured down this road. Maybe they started, but they probably started then stopped and turned around and ran away. This project has been in R&D for nearly 8 months and just as of today, finally went into production. We feel that functionality is equal to aesthetics, which is not always easy to accomplish when dealing with "from the ground up" projects. This is typically the reason for such long delays on new product development. Making something function is easy, making something look good while doing it adds an entire new array of potential issues. A lot of times it will come down to handling of the piece during production: How many different hands will it see on its way to the product box- The more hands, the more potential for error. This particular product sees several multi million dollar machines and several people. before hitting a box. Creating such a product in the manner in which it is derived, can be challenging to get it done without scratches and marring.
​
This is just the beginning of Dewla Dezign's new make and model lineup. We're excited.. I'm excited.
​
I am excited to bring new products to the market several times annually. Products that people will be excited to put on their dream cars. Products that separate themselves from the rest. Products that have true passion and desire written all over them.
​
Thanks to all of my customers thus far, and to all the customers of the future. I extremely appreciate your business for far too many reasons to express.
​
Thank you for allowing me to do something I am truly passionate about.
​
- Joe Lala
